מאת: ארבל ניסן, ניסטק
הבסיס להצלחה של מוצר אלקטרוני הוא תכנון בריא אשר מקיים תקשורת פתוחה ופורייה בין אנשי התכנון לאנשי הייצור על בסיס ידע וניסיון עבר. תכנון ועריכת מעגל אלקטרוני בצורה נכונה ליצוריות (DFM – Design for Manufacturing), מקצר את זמן היציאה לשוק, מפחית את עלויות ייצור המעגל ומשפר את תנובת הייצור DFM הינו תהליך שבמסגרתו מודעים מראש לתקלות אפשרויות שיכולות לצוץ בעתיד ומיישמים כבר כעת שיטות עבודה למניעת התרחשותן.
חברות הייטק המפתחות מוצרים אלקטרונים מחפשות תדיר דרך להוזלת המוצר ולקיצור זמן יציאתו לשוק. מוצר אלקטרוני שיוצא לשוק מהר יותר, בעלות נמוכה יותר הוא בעל יתרונות ברורים: מחזור חיי המכירות של המוצר מתארך, מושג חסכון בעלויות הפיתוח וכן נוצרת אפשרות להגיב מהר יותר לדרישת הלקוחות ולתמחר המוצר בצורה גמישה.
משימה זו כלל אינה פשוטה ומנהלים רבים מנסים לאתר כל דרך כדי לממש מטרה זו. אך לעיתים האפשרות לבצע זאת, הינה מאוד פשוטה ונמצאת ממש מעבר לפינה. תכנון נכון של המעגל האלקטרוני לייצוריות (DFM-Design for Manufacturing) מאפשר לקצר את זמן היציאה לשוק ולחסוך בעלויות הייצור של המוצר האלקטרוני.
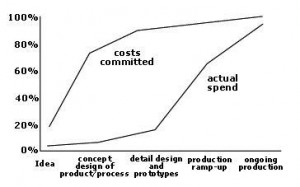
איור 1. עלות נקבעת לעומת עלות מבוצעת בתהליך תכנון מוצר אלקטרוני (מקור 2)
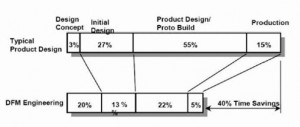
איור 2. תכנון נכון ליצוריות מאפשר לקצר בכ-40% את משך מחזור חיי התכנון והייצור של המוצר האלקטרוני (מקור 3)
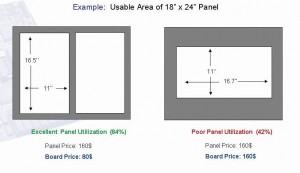
איור 3. ניצול אופטימלי של חומר הגלם מאפשר להוזיל את עלויות הייצור
מחקרים הראו (¹) כי חברות (Original Equipment Manufacturer) המפתחות מוצרים אלקטרונים, אשר יישמו שיטות DFM עמדו בתקציבי הפיתוח בשיעור של 82%, ביצעו בממוצע 66% פחות סבבי תיקון, וכן חסכו 26,000 $ בממוצע בסבבי התיקון שביצעו.
זאת ועוד, רוב העלות של המוצר האלקטרוני נקבעת עוד בשלב התכנון, לפני שהמוצר הגיע לייצור. חיבורים מדעים נוספים, (²) הראו שכ- 75-85% מעלות המוצר האלקטרוני נקבעת כבר במהלך התכנון, בעוד שההוצאות בפועל על המוצר גדלות בצורה ניכרת, דווקא לאחר שלב התכנון דהיינו בזמן הייצור. לאמור, שיקול נכון עוד במהלך התכנון של בעיות שיכולות להופיע בשלב הייצור וההרכבה, היא שיטה אפקטיבית ויעילה לחסכון בעלויות ולהעלאת תנובת הייצור.
כאמור החלטות בנושא תכנון קובעות את מרבית עלות המוצר האלקטרוני. ככל שתהליך הייצור מתקדם חלון האפשרות לביצוע שינויי תכנון קטן ועלות ביצוע השינוי גדלה בצורה אקספוננציאלית. לדוגמא, שינוי במוצר לאחר הרכבת אב הטיפוס טומן בחובו: סבב עריכה חדש, ביצוע שינוי הנדסי (ECO), הזמנת ח”ג נוספת, ייצור מחדש, בדיקות איכות ואמינות, עמידה בתקנים, פיגורים באספקות מול לקוחות ועוד. אמנם יתכן כי לאחר ביצוע האב טיפוס נרצה לבצע שינוי פונקציונאלי כלשהוא במוצר אך חייבים לדאוג לכך שהשינוי לא ינבע כתוצאה מבעיה יצוריות שנדרש להתמודד איתה, כזאת שיכלנו למנוע עוד בשלב התכנון. אורך מחזור חיי המוצר האלקטרוני, אשר מושפע מאיכות ואמינות המוצר, יכול להתנהל ולהתבצע בצורה אופטימאלית יותר כאשר קיימת סינרגיה בין אנשי הפיתוח העריכה והייצור אשר מודעים לנושא ומיישמים יחד שיטות DFM.
אמנם, יישום DFM דורש מהארגון השקעת זמן רבה יותר בשלב התכנון אך מחקרים הראו כי על אף שזמן התכנון מתארך, זמן ההוצאה לשוק (Time-To-Market) הכללי של המוצר יורד בכ- 40% בעקבות כך (³).
קיימים מספר תקנים המנחים בצורה מפורטת לגבי תכנון נכון של הכרטיס האלקטרוני, לדוג’ IPC2221-7. להלן מספר דוגמאות יישומים להמחשת הנושא.
1. תכנון כרטיס מלבני
בכל תכנון כרטיס אלקטרוני נדרש לחשוב על תהליך ייצורו, המטרה היא להתאים את המעגל האלקטרוני לפס הייצור עד כמה שניתן. במכונות קו הייצור קיימים מסועים אשר עליהם משונע הכרטיס במהלך העבודה. יש להקפיד כי הכרטיס יהיה מונח על המסועים בצורה יציבה וישמור על קשיחות מינימלית. כדי לאפשר חוזק מכני לכרטיס, יש לתכנן כרטיס סימטרי מלבני כאשר אורך הכרטיס גדול מרוחבו. כאשר רוחב הכרטיס גדול יותר מאורכו, יציבות הכרטיס בקו הייצור נפגמת. הלחץ המופעל על מרכז הכרטיס גבוה, ויכול לגרום לכיפוף הכרטיס במרכזו. יש לאפשר גם שוליים לכרטיס בעלי איזור נקי מרכיבים במרחק של 3 מ”מ, אשר ישמשו לתפיסת הכרטיס במסועים.
מעגלים בעלי צורות שאינן סימטריות מקשים מאוד על תהליכי הרכבת המעגל. במקרים אלו, יציבות הכרטיס בקו הייצור אינה גבוהה ולכן אמינות ודיוק השמת הרכיבים / מריחת הבדיל יהיו נמוכים. יתרה מכך, במהלך מחזור חיי הייצור של הכרטיס הוא לעיתים עובר דרך מכונות בהם נדרש לבצע ואקום לכרטיס (לדוג’ מכונת בדיקה חשמלית – ICT). ביצוע ואקום לכרטיס שאינו בתצורה סימטרית זו משימה מורכבת עד בלתי אפשרית. במעגלים אלו שומה עלינו לבצע השלמה מלאכותית למידת כרטיס מלבנית. השלמה זו תוסר במהלך הייצור לפני שליחת הכרטיס ללקוח.
2. גודל כרטיס אלקטרוני
חומרי הגלם לייצור הכרטיס האלקטרוני מגיעים בתצורה של פלטות בגדלים קבועים. יצרן ה- PCB חותך את פלטות חומר הגלם בהתאם למידות הכרטיס המיועד לייצור. ככל שהיצרן מנצל יותר את חומר הגלם כך עלות הכרטיס תהיה נמוכה יותר. לדוג’: מרבית היצרנים עובדים עם חומר גלם במידות של “18 על “24. איור 3 מדגים איך שינוי של 0.2’’ באורך הכרטיס מביא להוזלת הייצור ב- 50%. מומלץ להתייעץ עם יצרן ה- PCB כדי לבדוק באילו מידות חומרי גלם הוא משתמש וכיצד ניתן לנצל בצורה מקסימאלית מידות אלו.
3. תכנון פנלזיציה
תכנון פנליזציה יכול להוזיל משמעותית את תהליך ייצור הכרטיס האלקטרוני. תכנון הפנל מאפשר מחד לשמור על מידת הכרטיס הגנרי ומאידך לנצל בצורה אופטימאלית את פס הייצור. ניתן לתכנן פנל המכיל מספר כרטיסים קטנים. בשיטה זו הפנל יורכב בקו הייצור ולאחר מכן יפורקו הכרטיסים ממנו להמשך העבודה. משך הזמן שהמכונות יעבדו על כרטיס בודד כאשר הוא נמצא בפנל יהא קצר משמעותית מאשר הוא מופיע ככרטיס בודד, גם אם ניקח בחשבון את משך פירוק הכרטיס מהפנל לאחר ההרכבה כדי להחזירו למצבו הגנרי. פעולה זו מאפשרת לנצל בצורה טובה יותר את מכונות הייצור ובכך להוזיל את עלות העבודה. החיסכון הוא משמעותי יותר כאשר מדובר על הרכבות בסדרות גדולות. העבודה עם פנל של מספר כרטיסים מייעלת גם את העבודה הידנית על הכרטיס, כגון ההלחמות הידניות, וכן את הבדיקות החשמליות כך שבמחזור בדיקות בודד של פנל נבדקים מספר כרטיסים. אלמנט שראוי לבחון בתכנון פנל היא רמת הדיוק בייצור הפנל. בפנלים ארוכים רמת הדיוק (Tolerance) של הכרטיס הבודד, מוכפלת לכל הכרטיסים לאורך הפנל וגוררת תזוזה הולכת וגדלה בפדים. סטייה זו, המורגשת בעיקר בכרטיסים הממוקמים בסוף הפנל, יכולה לפגום בעבודה על הכרטיס בתחנות הייצור לדוג’ במריחת הבדיל. בפנל בעל אורך או רוחב של מעל “12, התזוזה המצרפית יכולה להגיע ל “0.003, זו תזוזה גדולה מידי אם רוצים להרכיב רכיב עם Pitch של “0.02 ב- Yield גבוה.
תכנון פנל בצורה נכונה חייב להביא בחשבון מצד אחד את חוזק ויציבות הפנל במהלך שינועו בקווי הייצור ומצד שני יש לתכנן את הפנל כך שהפרדת הכרטיסים ממנו תתבצע בקלות וביעילות תוך שמירה על איכות מקסימלית. ההפרדה בין הכרטיסים על פני הפנל צריכה להתבצע בצורה הנוחה והמהירה ביותר. ישנן שתי שיטות מרכזיות לכך: א. V-CUT ב. Break-Away Tabs.
א. V-CUT (ידוע גם בשם V-GROOVE) – מתכננים חריצים על פני הפנל במקומות המיועדים להפרדה. פירוק הכרטיסים מהפנל מתבצע באמצעות התקן בעל שני סכיני חיתוך מעוגלים, העומדים אחד מעל השני (ויוצרים שתי צורת V) ובטווח מעבירים את חריצי הפנל. יש לשים לב למספר פרמטרים בתכנון חריץ זה: עובי המעגל, עומק החריץ משני צידי המעגל, עובי המעגל הנותר, רוחב החריץ, זווית החריץ.
ב. Break-Away Tabs – בשיטה זו, ממקמים מספר חורים קטנים (Break-Away Tabs) בין שני אזורים המיועדים להפרדה, ופירוק המעגלים מבוצע בעזרת שבירה ידנית או ממוכנת. יש לשים לב למספר פרמטרים: קוטר החור, אורך החור, מרחק בין החורים, כמות החורים, מרחק החורים מקצה המעגל. כדי לחסוך בעלות הייצור בנקודה זו, ניתן לתכנן את קוטר החור בהתאם לקוטר חור המעבר (VIA) הקטן ביותר.
מומלץ לעיין בתקן IPC-2221 המפרט כיצד לתכנן את הפרמטרים של שתי השיטות.
שיטה ה- VCUT עדיפה על שיטת Break-Away Tabs מכמה סיבות: 1) מהירות הפרדה 2) אמינות גבוהה 3) התעסקות ידנית מינימלית 4) עלות נמוכה.
יחד עם זאת בשיטת ה- VCUT יש לשים לב למספר דגשים
a. יש לשמור על מרחק נקי מרכיבים (Clearance) של 1.5 מ”מ מחריץ ה- V-CUT כדי לא לפגוע בהם במהלך החיתוך. כמו-כן יש לוודא כי הרכיבים הממוקמים בסמוך לחריץ החיתוך יהיו בעלי חוזק מספיק כדי לעמוד בלחץ המכאני המופעל באזור במהלך החיתוך.
b. כאשר רוחב הכרטיס הינו למעלה מ-10 ס”מ, לא ניתן לתכנן פנל בעל שני טורים עקב חוסר יציבות הפנל במרכזו, ולכן נעדיף לתכנן פנל בעל טור אחד כדי למנוע כיפוף ו”יצירת בטן” במרכז הפנל במהלך מעבר הפנל בתנור ההלחמה (REFLOW).
במעגלים מסוימים לא ניתן לבצע את שיטה ולכן ה- VCUT נשתמש בשיטת ה- Break-Away Tabs
i. לדוגמא כאשר משתמשים בקונקטור מסוג SMT אשר בולט מהכרטיס האלקטרוני לא ניתן יהיה להפריד את המעגלונים כיוון שהרכיב חוצה את החריץ המיועד לחיתוך. (איור 4) במקרים אלו שומה עלינו להשתמש בשיטה ב’. במקרה זה כדי לאפשר שבירה נוחה והפרדה של הכרטיס, יש לוודא שחורי השבירה לא ימוקמו מתחת לרכיב הבולט.
ii. יש לדעת כי לא ניתן לייצר כרטיס אשר חריץ ה- V-CUT שלו מגיע עד אמצע המעגל. יש לוודא כי לכל חריץ יש שתי קצוות חופשיות בקצה המעגל.
iii. כאשר עובי הכרטיס קטן מ- 1.6 מ”מ, שימוש בשיטה א’, יערער את יציבות הכרטיס במהלך הייצור. כיוון שבשיטה זו, חומר הגלם שנשאר בתוך החריץ מהווה 1/3 מעובי הכרטיס, בכרטיסים בעלי עובי נמוך, חומר הגלם יהיה צר מאוד וקשיחות הכרטיס תיפגם.
4. מיקום רכיבים קריטיים
היבט חשוב ביותר בשלב התכנון אשר יש לו השלכות מהותיות על איכות המעגל לאחר הייצור, הוא מיקום רכיבים קריטיים, כגון: BGA, Fine-Pitch, Mictor.
BGA .a
i. איזון טרמי – רכיב ה- BGA אוגר בתוכו חום רב במהלך ההלחמה ולכן חשוב לוודא כי קיים איזון טרמודינמי על פני הכרטיס האלקטרוני. התפשטות א-סימטרית של חום יכולה לגרום לעיוותים בכרטיס, פגיעה ברכיבים רגישים ותוצאות הלחמה שאינם איכותיות. במעגלים בעלי BGA בודד מומלץ להרכיבו במרכז כדי לאפשר שחרור חום אופטימלי ואחיד על פני המעגל. בכרטיסים בעלי מספר רכיבי BGA מומלץ למקמם בנקודות ייחוס סימטריות על פני המעגל. במעגלים המורכבים בתהליך תואם LEAD FREE החום גבוה יותר, ולכן משמעות האיזון הטרמי קרדינלית להרכבת המעגל. בנוסף לא מומלץ למקם רכיבי BGA בשפת הכרטיס כי אזורים אלו נוטים להיות קרים יותר במהלך ההלחמה. כמו-כן, סמוך לרכיבי TH החוזק המכני של הכרטיס נמוך יותר ולכן לא מומלץ למקם באזור רכיבי BGA
REWORK .ii – כדאי להשאיר שטח נקי ללא רכיבים של 3 מ”מ מסביב לרכיב ה- BGA כדי לאפשר פירוק אופטימלי בביצוע פעולת REWORK. במכונות REWORK הפועלות ע”י קרן אינפרא אדום מספיק לשמור על מרחק של 1 מ”מ.
iii. בדיקת X-Ray – במעגלים בעלי 2 צדדים (Double Sided Reflow) כדאי להשאיר את הצד שמקביל לרכיב ה- BGA נקי מרכיבים כדי לאפשר בדיקה אמינה של X-Ray. רכיבים הממוקמים בצד שני של המעגל המקביל למיקום ה- BGA, נראים בתהליך הרנטגן ויכולים להטעות את תוצאות בדיקת הלחמת הרכיב.
Fine Pitch .b
טיפול ברכיבי FP בפס הייצור מחייב דיוק קפדני. לכן לא מומלץ למקם רכיבים אלו קרוב לשפת המעגל, כי באזור זה יתכנו עודפי בדיל בזמן מריחת המעגל בעיקר במכונות מריחה אוטומטיות.
MICTOR .c
רכיב זה מורכב בקווי ה- SMT לפני הכנסת הכרטיס לתנור ההלחמה. כדי לאפשר נגישות מיטבית להנחת הרכיב, יש למקמו קרוב לשפת המעגל, כ- 15 מ”מ עד הפד הקרוב ביותר. רכיבי MICTOR ארוכים, למעלה מ- 50 מ”מ, יש למקם לאורך המעגל, בכיוון תנועת הכרטיס בתנור ההלחמה. הדבר נובע כתוצאה מכיפוף המעגל בשלב ההלחמה בתנור, אשר יכול לגרום לחוסר מגע בין מרכז הרכיב לכרטיס האלקטרוני.
5. מרווח בין רכיבים
במיקום הרכיבים במעגל המודפס, יש לשמור על מרווח מינימלי בין אריזה אחת למשנה. מומלץ לעיין בתקן IPC2221 המגדיר את שמירת המרחקים הרצויה. צפיפות גבוהה מידי של רכיבים יכולה לגרום לתנובת ייצור Yield נמוכה. לא זו אף זו, במקרים מסוימים ביצוע השלמות ותיקונים למעגלים Rework & Repair הינו בלתי אפשרי. כמו-כן, מיקום צפוף מידי, מקשה על תהליך ביקורת האיכות הויזואלית הן הידנית והן האוטומטית במכונות ה- AOI.
תכנון המעגל צריך לכלול מרווח מספיק בין רכיבים כדי לאפשר שימוש מיטבי במלחם. מיקום רכיבים צפופים מידי עלול להקשות למנוע גישה של מלחם לטובת ביצוע תיקונים ושינויים במעגל. בעריכת המעגל ראוי לתכנן נגישות ידנית קלה ומהירה לרכיבים אלו. כלל האצבע הוא לשמור על מרחק בשיעור הרכיב הגבוה מבין שני רכיבים סמוכים.
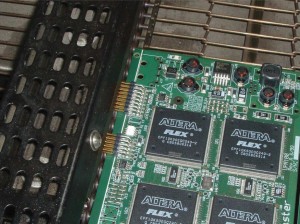
איור 4. הכרסום חותך את גוף הקונוקטורים ולכן לא ניתן להפריד את השוליים ללא הסרת הקונוקטורים והרכבתם ידנית
6. תכנון בהתאם לתהליכי הייצור וההרכבה
את הכרטיס האלקטרוני חשוב להתאים במידת האפשר לתהליכי הייצור וההרכבה שלו. תכנון נכון של הכרטיס במסגרת זו, יסייע לייצור מהיר ללא תקלות ובעקבות כך גם להפחתת עלות המוצר. יש להעדיף למקם רכיבים בצד אחד בלבד של הכרטיס. כרטיס המכיל רכיבי SMT משני צידיו עובר פעמיים את תהליך הייצור. מיקום רכיבים בצד בודד, מקצר בכמעט פי שניים את זמן העבודה על הכרטיס במהלך הרכבתו וכן חוסך עלות כלים ייעודיים (לדוג’ Stencil). כיוון שכורח המציאות לרוב לא מאפשר מיקום רכיבים בצד אחד בלבד, לדוג’ כתוצאה מצפיפות, רצוי למקם רכיבים חריגים בצד ה- C.S לדוג’ רכיבי TH, ICs, FP, Oscillators, רכיבים גבוהים, רכיבים כבדים, רכיבים רגישים. רכיבים אלו יכולים להינזק במהלך הייצור כאשר הם ממוקמים בצד ה- P.S, גם בעקבות העובדה שצד ה- P.S עובר פעמיים את תהליך ההלחמה בתנור ה- Reflow. בצד ה- P.S מומלץ למקם רכיבים פאסיביים, כגון נגדים קבלים אשר עמידים יותר בתנאי ייצור אלו.
דבר נוסף, כאשר משתמשים ברכיבים מסוג TSOP ,SOIC יש למקמם כך שמריחת הבדיל במכונת ה- PRINTER תתבצע לאורך הפדים שלהם, דבר אשר ימנע קצרים בין רגלי הרכיבים. כאשר נדרש להשתמש בקונקטורים מסוג SMT הבולטים משפת הכרטיס, יש לתכנון שוליים ייעודיות לכרטיס אשר יתמכו ברכיב ובנוסף ניתן יהיה להפרידם לאחר ההרכבה.
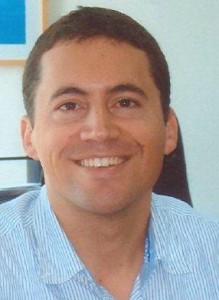
ארבל ניסן, ניסטק
6. תכנון לבדיקתיות AOI X-RAY
התחום של תכנון לבדיקתיות מהווה גורם הנדסי חשוב ביותר בתכנון מעגלים מודפסים. המטרה היא לתכנן את הכרטיס כך שהבדיקה החשמלית תהיה יעילה ומהירה. תחום זה מתחלק לשני חלקים, תכנון חשמלי ותכנון פיזי. בתכנון החשמלי נבחנים שיטות הבדיקה שינקטו, אלו אפליקציות יבדקו ועוד. בתכנון הפיזי מובאים לידי ביטוי התאמת הכרטיס להתקן הבדיקה ומיקום נקודות הבדיקה. בנקודה זו אתייחס לשני התקני בדיקה שנוספו בשנים האחרונות, AOI ו- XRAY.
a. מכונת ה- AOI מבצעת בדיקה ויזואלית של הכרטיס. המכונה מצלמת את הכרטיס וע”י כך מאתרת תקלות. כדי שבדיקה זו תהיה יעילה ואפקטיבית נדרש להקפיד על סימון עקבי על המעגל, לדוג’ גופן זהה עובי וצורה, צבע כרטיס, רישומים עקביים וכן ציון קוטביות רכיבים בצורה ברורה. סימון לא עקבי גורם לזמן הבדיקה להתארך ומגדיל שלא לצורך את בסיס הנתונים במכונת ה- AOI. כמו-כן כדי לאפשר צילום מיטבי במכונה מומלץ לשמור על שטח פתוח בעל זווית פריסה של 35°-65° מכל רכיב כדי לאפשר למצלמות ה-AOI לאתר במהירות ובקלות את הרכיבים.
b. מכונת ה- XRAY מבצעת בדיקה לכרטיס האלקטרוני. המכונה מיועדת בעיקר לצילום רכיבי BGA, QFN. בדיקה זו לעיתים מבוצעת בצורה אוטומטית, בעיקר בכרטיסים מרובי BGAs, לאחר הגדרת המיקום ותצורת הרכיב. על-מנת שבדיקה זו תתבצע בצורה מיטבית יש לוודא כי נקודות הייחוס (fiducial) יהיו ברורות וקלות לאיתור ע”י המכונה. כיוון שקרן הרנטגן חודרת לכל עובי הכרטיס, יש לשמור על אזור נקי משני צידי הכרטיס עבור נקודות הייחוס. כמו-כן, יש לוודא כי כאשר ממקמים רכיבי BGA משני צידי הכרטיס, לא למקמם אחד מתחת לשני, דבר שיקשה על בדיקת טיב ההלחמה במגונת ה- XRAY.
7. סימון ברור ולוגי על פני המעגל
סימון נכון על פני המעגל מסייע לייצור יעיל ומהיר של הכרטיס האלקטרוני. הדבר מועיל הן למכונות האוטומטיות, לדוג’ AOI והן לעבודה הידנית המבוצעת על הכרטיס, לדוג’ ביקורת איכות, בדיקה חשמלית, Rework & Repair.
ראשית נדרש לוודא כי הרכיבים מסודרים בסדר לוגי ועקבי לפי סימונם, על פני משטח המעגל, כדי שבמידת הצורך ניתן יהיה לאתר בקלות את מיקומם במהלך הייצור. סימון זה של הרכיבים צריך להיות ברור ושלם ולא מוסתר ע”י פדים וחורים מכניים. יש לוודא כי גם לאחר השמת הרכיב בכרטיס הסימון נותר גלוי. בנוסף ברכיבים מרובי רגלים חובה לציין את רגל מספר “1” סמוך לפד הרלוונטי, וכן כדאי להוסיף ליד כל רגל עשירית את מספרה כדי לאפשר איתור מהיר של רגלי הרכיב. ברכיבים בעלי קוטביות נדרש לסמן “+” המתאר את כיוון השמת הרכיב וכן את כיוון הזרם החשמלי ברכיבי דיודות.
8. תכנון נקודות ייחוס (Fiducial)
נקודות הייחוס המצוינות על הכרטיס האלקטרוני משמשות את המכונות האוטומטיות בקו הייצור. מיקום נכון של נקודות הוא קרדינאלי בהצלחת ייצור הכרטיס כיוון שבהתאם לנקודות אלו, מבצעות המכונות את פעולתם המדויקת כגון: השמת רכיבים, מריחת בדיל, בדיקת ויזואליות (AOI). הצורך בסעיף זה מקבל משנה חשיבות, כאשר קיימת מגמה הולכת וגוברת של מזעור המוצר האלקטרוני כך שלכל סטייה של מיל ישנה השלכה מכרעת. לכן חשוב להקפיד על מספר כללים בתכנון נקודות הייחוס בכרטיס. ראשית יש לאפשר שחרור Soldermask, אשר ימנע את הסתרת הנקודה, אלמנט אשר יפחית את דיוק ההשמה. יש למקם 3 נקודות ייחוס לפחות על שטח הכרטיס אשר צריכות להופיע בצורה א-סימטרית כדי לאפשר למכונה האוטומטית לזהות בצורה חד-חד ערכית כי המעגל הוכנס למסוע המכונה בכיוון הנכון. יש להימנע מלמקם את הנקודות בשולי הכרטיס (מרחק מינימום של “0.25) וכאשר מדובר על פנל (ראה סעיף 3) יש למקם את ה- Fiducial על הכרטיס עצמו ולא רק על הפנל. לטובת שימוש במכונות מריחת בדיל (Printer) אוטומטיות יש למקם נקודות ייחוס גם על קבצי ה- SolderMask וה- SolderPaste. כמו-כן, כדי שנקודת הייחוס תהיה ברורה וקלה לזיהוי במהלך שימוש במכונת ה- X- RAY, יש לשמור על אזור נקי מהצד השני של הכרטיס עבור נקודות הייחוס כיוון שקרן הרנטגן חודרת לכל עובי הכרטיס (סעיף 7).
10. עובי כרטיס
פרמטר נוסף שראוי לבחון אשר הוא בעל השלכות על ייצור הכרטיס הוא העובי. עובי הכרטיס המתאים ביותר לעבודה בייצור הוא 1.6mm וראוי עד כמה שניתן לתכנן בהתאם למידה זו.
כאשר מדובר על מידת עובי של 1mm ומטה, הדבר מצריך טיפול מיוחד. ככל שעובי הכרטיס יורד כלפי מטה כך קשיחות הכרטיס נמוכה ויציבותו במהלך הייצור נפגמת. בכרטיסים אלו נדרש לתכנן תמיכה במהלך הייצור. כאשר קיימים רכיבים בצד אחד בלבד, ניתן להוסיף פלטת תמיכה מתחת לכרטיס אשר תשמור על יציבותו. במקרה והרכיבים ממוקמים על הכרטיס משני צידיו, יש לתכנן התקן מיוחד ייעודי עבור הכרטיס אשר יתמוך בכרטיס במהלך שינועו בקווי הייצור. התקן זה, מייקר משמעותית את עלות הייצור (במנות ייצור גדולות תוספת העלות תהיה זניחה יותר) וכן מאריך את זמן האספקה, לכן עדיף למקם רכיבים בצד אחד בלבד. בתכנון פנל בעל עובי של 1mm ומטה, צריך להתייחס לתצורת הפרדת כרטיסים. במקרה זה לא ניתן להשתמש בשיטת ה- V-CUT העדיפה (ראה סעיף 3) אלא נאלץ להשתמש בשיטת ה- Break Away. מנגד, כרטיסים אלקטרונים בעלי מידת עובי גבוהה, של 2mm ומעלה מאלצים טמפרטורה גבוהה במהלך הייצור. ככל שעובי הכרטיס גבוה יותר כך נדרש לקבוע רמת חום גבוהה יותר. טמפ’ הלחמה גבוהות יכולות לגרום נזקים לרכיבים רגישים, למצע המעגל ולפיזור החום בשטח הכרטיס. במקרים אלו, מומלץ להתייעץ עם יצרן/מרכיב המעגל כדי לאפשר ייצור מיטבי.
לסיכום, בשלב תכנון ועריכת הכרטיס האלקטרוני חייבים להתחשב בשיקולי ייצור והרכבת המעגל. תכנון נכון ליצוריות מקצר את זמן היציאה לשוק (Time-To-Market), מוזיל את עלות הייצור ובסופו של יום מניב רווחים טובים יותר לחברה. פעולות מסוימות בשלב התכנון כגון: מיקום רכיבים BGA, תכנון פנל לכרטיס, מיקום נק’ ייחוס, תכנון לבדיקתיות ועוד, הן בעלי השלכה משמעותית על הצלחת ייצור המוצר האלקטרוני. המהנדסים ועורכי המעגלים המודפסים חייבים להיות ערים ולהכיר היטב את קווי הייצור ואת שלבי-המעבר של המוצר עד להשלמתו הסופית. סינרגיה בין החברה המבצעת את עריכת הכרטיס האלקטרוני ובין החברה המייצרת ומרכיבה אותו תבטיח ללקוח שהדבר הנכון יבוצע בצורה הנכונה בפעם הראשונה.
מקורות
(¹) Aberdeen Group, Printed Circuit Board Design Integrity. The Key to Successful PCB Development 2007. http://www.marketwire.com/mw/rel.jsp?id=730231
(2) Martin Tarr, The DfX concept.
http://www.ami.ac.uk/courses/topics/0248_dfx/index.html
(3) Carter, D. E., Baker, B. S., Concurrent Engineering: The Product Development Environment for the 1990s, Addison-Wesley 1992.