תכנון מעגל אלקטרוני בצורה מתאימה לייצור, מאפשר לשפר את איכות ואמינות המעגל האלקטרוני, לקצר את זמן היציאה לשוק ואף לחסוך בעלויות הייצור.
איך עושים זאת? להלן 7 כללים שמומלץ להכיר טוב בעת פיתוח כרטיס אלקטרוני.
1. גודל ותצורת הכרטיס
1. 1 התאמת גודל הכרטיס האלקטרוני למידת חומר הגלם של היצרן – חומרי הגלם לייצור הכרטיס האלקטרוני מגיעים בתצורה של פלטות בגדלים קבועים. היצרן חותך את חומר הגלם בהתאם למידות הכרטיס המיועד לייצור. עלות חומר הגלם הינה כ-30% מעלות ייצור הכרטיס. ככל שהיצרן מנצל בצורה יעילה יותר את חומר הגלם, כך עלות הכרטיס תהיה נמוכה יותר. לדוג’: מרבית היצרנים עובדים עם חומר גלם במידות של ”18 על ”24. איור 1 מדגים איך שינוי של 0.2” באורך הכרטיס מביא לניצול אופטימלי של חומר הגלם ובעקבות כך להוזלת ייצור הכרטיס במידה ניכרת. מומלץ להתייעץ עם יצרן הכרטיס כדי לבדוק באילו מידות חומרי גלם הוא משתמש וכיצד ניתן זאת בצורה מרבית.
1.2 לוודא מינימום ומקסימום של מידות המעגל– למכונות האוטומטיות המשמשות לייצור והרכבת המעגל קיימות מגבלות פיזיות של מידות כרטיס. לדוג’ מכונות הרכבה בטכנולוגית SMT, יכולות להרכיב כרטיס באורך של בין 60-508 מ”מ ורוחב בין 60-450 מ”מ.
1.3 לשמור על יציבות המעגל בקווי ההרכבה– בקווי ההרכבה קיימים מסועים אשר עליהם משונע הכרטיס במהלך העבודה. יש להקפיד כי הכרטיס ממוקם על המסועים בצורה יציבה ושומר על קשיחות מינימלית. כדי לאפשר חוזק מכני לכרטיס בתהליך ההרכבה, יש לתכנן כרטיס סימטרי מלבני כאשר אורך הכרטיס גדול מרוחבו. כאשר רוחב הכרטיס גדול יותר מאורכו, יציבות הכרטיס בקו הייצור נפגמת. הלחץ הגבוה המופעל על מרכז הכרטיס, יכול לגרום לכיפוף הכרטיס בתהליך ההרכבה. כמו-כן, רצוי לשמור על אזור נקי מרכיבים לאורך קצוות הכרטיס בשיעור של 5 מ”מ אשר ישמשו לתפיסת הכרטיס במסועים. במידה וזה לא ניתן, חייבים להוסיף שוליים לאורך הכרטיס. מעגלים בעלי צורות שאינן סימטריות מקשים מאוד על תהליכי הרכבת המעגל. במקרים אלו, יציבות הכרטיס בקו הייצור אינה גבוהה ולכן אמינות ודיוק השמת הרכיבים /מריחת הבדיל יהיו נמוכים. במעגלים אלו שומה עלינו לבצע השלמה מלאכותית למידת כרטיס מלבנית. השלמה זו תוסר במהלך הייצור לפני שליחת הכרטיס ללקוח.
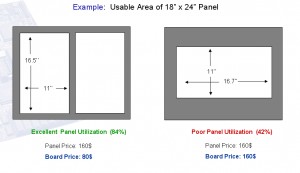
איור 1 – ניצול אופטימלי של חומר הגלם מאפשר להוזיל את עלויות הייצור. קרדיט: ניסטק דיזיין
2. תכנון פנליזציה
תכנון הפנל מטרתו להתאים את מידות הכרטיס האלקטרוני לקו הייצור. פעולה זו מאפשרת מחד לשמור על מידת הכרטיס הגנרי ובה בעת, להתאימה בצורה אופטימאלית ויעילה לפס הייצור. ניתן לתכנן פנל המכיל מספר כרטיסים קטנים. בשיטה זו הפנל יורכב בקו הייצור ולאחר מכן יפורקו הכרטיסים ממנו להמשך העבודה. משך הזמן שהמכונות יעבדו על כרטיס בודד כאשר הוא נמצא בפנל יהא קצר משמעותית מאשר הוא מופיע ככרטיס בודד, גם אם ניקח בחשבון את משך פירוק הכרטיס מהפנל לאחר ההרכבה כדי להחזירו למצבו הגנרי. בצורה זו, נוכל לנצל בצורה טובה יותר את מכונות הייצור ובכך להוזיל את עלות העבודה. החיסכון הוא משמעותי יותר כאשר מדובר על הרכבות בסדרות גדולות. העבודה עם פנל של מספר כרטיסים מייעלת גם את העבודה הידנית על הכרטיס, כגון ההלחמות ידניות, וכן את הבדיקות החשמליות כך שבמחזור בדיקות בודד של פנל נבדקים מספר כרטיסים בו זמנית. תכנון פנל בצורה נכונה, חייב להביא בחשבון מצד אחד את חוזק ויציבות הפנל במהלך שינועו בקווי ההרכבה ומצד שני יש לתכנן את הפנל כך שהפרדת הכרטיסים ממנו לאחר ההרכבה תתבצע בקלות וביעילות. ההפרדה בין הכרטיסים על פני הפנל צריכה להתבצע בצורה הנוחה והמהירה ביותר. ישנן שתי שיטות מרכזיות לכך: א. V-CUT ב. Break-Away Tabs. יש להכיר היטב את היתרונות והחסרונות של כל שיטה כדי לבחור באיזו שיטה לבחור. מומלץ לעיין בתקן IPC-2221 המפרט כיצד לתכנן את הפרמטרים של שתי שיטות אלו.
3. מיקום רכיבי BGA
רכיב ה- BGA (Ball Grid Array) יש לו מעמד מיוחד בתהליך הרכבת הכרטיס. יש לכך מספר סיבות: א. כיוון שרכיב ה BGA בדרך כלל הינו בעל גוף מאסיבי, נדרשת אנרגיה גבוהה יותר לטובת הלחמתו ביחס לרכיבים אחרים. ב. במידה ונרצה לפרקו מהכרטיס בהמשך, לא ניתן לבצע זאת בצורה ידנית כמו יתר הרכיבים אלא במכונה ייעודית ג. בדיקת הלחמת רכיב ה BGA מבוצעת באמצעות מכונת רנטגן (X-RAY) בשונה ממרבית הרכיבים האלקטרוניים בכרטיס ד. עלות רכיב ה- BGA לרוב גבוהה משמעותית מיתר שכניו במעגל. תהליך הלחמה של הכרטיס האלקטרוני מתבצע בטמפרטורות גבוהות של כ- 245-250 מעלות צלזיוס. בתהליך זה, שומה עלינו לוודא כי קיים איזון טרמודינמי על פני שטח הכרטיס האלקטרוני. לאור מגוון הרכיבים המורכבים בכרטיס האלקטרוני, קיימת שונות תרמית גבוהה על פניו. הפרש טמפרטורה חריג בין שתי נקודות על פני הכרטיס האלקטרוני בתהליך ההלחמה עלול להוביל למצב של עיוות הכרטיס בתנור ההלחמה, קצרים, נתקים ואף כרטיס מעוות ביציאה מקו הייצור. רכיב ה BGA כתוצאה מאופיו, מולחם בטמפרטורה גבוהה באופן ניכר ביחס להלחמת יתר הרכיבים במעגל האלקטרוני לכן יש לשים לב היטב למיקום רכיב ה BGA בכרטיס האלקטרוני. במעגלים בעלי BGA בודד מומלץ להרכיבו במרכז הכרטיס כדי לאפשר שחרור חום אופטימלי ואחיד על פני המעגל. בכרטיסים בעלי מספר רכיבי BGA, מומלץ למקמם בנקודות ייחוס סימטריות על פני המעגל כדי לוודא איזון טרמודינמי על פני שטח הכרטיס. בנוסף, מומלץ לא למקם רכיבי BGA בשפת הכרטיס מאחר ואזורים אלו נוטים להיות קרים יותר במהלך ההלחמה. כאמור, פירוק רכיב ה BGA במידת הצורך לאחר ההרכבה, מתבצע במכונה ייעודית. לכן כדי לאפשר פירוק זה בעתיד, יש להשאיר שטח נקי ללא רכיבים של 3 מ”מ מסביב לרכיב ה- BGA. זאת ועוד, בכרטיסים אלקטרוניים המכילים רכיב BGA משני הצדדים (דבר שעקרונית לא מומלץ לבצע רק אם כלו כל הקיצין), מומלץ לוודא כי רכיבי ה- BGA לא ממוקמים אחד מתחת השני כדי לאפשר בדיקה אמינה של הרכיב במכונת הרנטגן (X-Ray). רכיבי BGA הממוקמים בשני צידי הכרטיס האלקטרוני, אחד מתחת לשני, נראים בתהליך הרנטגן ויכולים להטעות את תוצאות בדיקת הלחמת הרכיב.
4. מרווח בין רכיבים
למיקום הרכיבים בכרטיס האלקטרוני, ישנו משנה חשיבות בהצלחת הרכבתו בקו הייצור. יש לשמור על מרווח מינימלי בין אריזת רכיב אחת למשנה. צפיפות גבוהה מידי של רכיבים, עלולה לגרום לתנובת ייצור (Yield) נמוכה. לא זו אף זו, במקרים מסוימים, ביצוע השלמות ותיקונים למעגלים עם רכיבים בסמיכות קרובה מידי, הינה משימה כמעט בלתי אפשרית. במעגלים בעלי המרווח בין הרכיבים אינו מספק, תהליך ביקורת האיכות הוויזואלית הן הידנית והן האוטומטית במכונות ה- AOI, עלול לא להיות מיטבי. ככלל אצבע, מרכיבים קטנים (כגון 0402 ומטה) מומלץ לשמור על מרחק מינימלי של 10 מיל. מרכיבים גדולים (BGA, קונקטורים וכו’) מומלץ לשמור על מרחק של מינימום 30 מיל. תקן IPC2221 מגדיר את שמירת המרחקים הרצויה בין הרכיבים בכרטיס האלקטרוני.
5. תכנון בהתאם לתהליכי הייצור וההרכבה
את הכרטיס אלקטרוני חשוב להתאים במידת האפשר לתהליכי הייצור וההרכבה שלו. תכנון נכון של הכרטיס במסגרת זו, יסייע לייצור מהיר ללא תקלות ובעקבות כך גם להפחתת עלות המוצר. ככלל, יש להעדיף למקם רכיבים בצד אחד בלבד של הכרטיס. כרטיס המכיל רכיבי SMT משני צדדיו עובר פעמיים את תהליך ההלחמה. מיקום רכיבים בצד בודד, מקצר בכמעט פי שניים את זמן העבודה על הכרטיס במהלך הרכבתו וכן חוסך עלות כלים ייעודיים (לדוג’ מסכת הלחמה – Stencil). כיוון שכורח המציאות לרוב לא מאפשר מיקום רכיבים בצד אחד בלבד של הכרטיס האלקטרוני, רצוי למקם רכיבים חריגים בצד ה- C.S לדוג’ רכיבי TH, IC, FP, Oscillators, BGA, רכיבים גבוהים, רכיבים כבדים, רכיבים רגישים. רכיבים אלו יכולים להינזק במהלך הייצור כאשר הם ממוקמים בצד ה- P.S, גם בעקבות העובדה שצד ה- P.S עובר פעמיים את תהליך ההלחמה בתנור ה- Reflow. בצד ה- P.S לעומת זאת, מומלץ למקם רכיבים פאסיביים, כגון נגדים קבלים אשר עמידים יותר בתהליך ההלחמה. רכיבים מסוג TH ניתן להלחים היום גם במכונות SMT אוטומטיות ויש לכך יתרונות רבים. הרכבת רכיב TH בקו הרכבות אוטומטי SMT הינה מהירה קרוב לפי 10 מאשר הרכבתו בשיטות החלופות שהינן ידניות או חצי אוטומטיות. בנוסף, לאור זאת שקו הרכבות SMT הינו אוטומטי, העלות להרכבת רכיב TH בקו זה הינה נמוכה בכמעט פי 4 בהשוואה להרכבת רכיב TH בשיטות המסורתיות. לכן, מומלץ לתכנן את הרכבת רכיב ה TH בקו ה SMT האוטומטי. לצורך כך, יש להתייחס לרכיב ה TH בדומה לרכיב ה SMT כלומר יש להגדיר לו פתחים במסכת הבדיל (Stencil) דרכם יעבור משחת ההלחמה לחורים במעגל המודפס (איור 2). בהגדרת המידות של פתחים אלו יש להתחשב במספר פרמטרים ביניהם: עובי המעגל, אורך פיני רכיב ה TH וכן קוטר החור במעגל. יש לוודא בדפי הנתונים של רכיב ה TH, שהינו עמיד בטמפרטורת ההלחמה בקו ה SMT (עד כ- 260 מעלות צלזיוס).
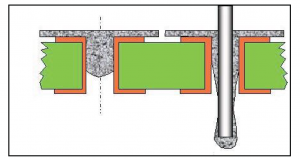
איור 2: הלחמת רכיב TH בקו הרכבות אוטומטי SMT מאפשרת להוזיל את עלות הרכבת הכרטיס האלקטרוני ואף לשפר את איכות ההלחמה. קרדיט: ניסטק דיזיין
6. תכנון נקודות ייחוס (Fiducial)
נקודות הייחוס המצוינות על הכרטיס האלקטרוני משמשות את המכונות האוטומטיות בקו ההרכבה. מיקום והגדרה נכונה של נקודות אלו הוא קרדינאלי באיכות הרכבת הכרטיס. בהתאם לנקודות אלו, מבצעות המכונות את הפעולות המדויקת כגון: השמת רכיבים, מריחת בדיל, בדיקת ויזואלית (AOI). הצורך בכך מקבל תוקף נוסף, כאשר המגמה למזעור המוצר האלקטרוני, רווחת יותר ויותר. בכרטיסים אלקטרוניים צפופים, כל סטייה מזערית בדיוק השמת הרכיב, עלולה להיות בעלת השלכה מכרעת על איכות ואמינות הכרטיס. לכן חשוב להקפיד על מספר כללים בתכנון נקודות הייחוס בכרטיס. ראשית יש לאפשר שחרור Soldermask, אשר ימנע את הסתרת נקודת הייחוס ויאפשר למכונה קו הייצור האוטומטית זיהוי מהיר, ברור ומדויק של הנקודה. יש למקם 3 נקודות ייחוס על שטח הכרטיס בצורה א-סימטרית כדי לאפשר למכונה האוטומטית לזהות בצורה חד-חד ערכית כי המעגל הוכנס למסוע המכונה בכיוון הנכון. יש להימנע מלמקם את הנקודות בשולי הכרטיס (מרחק מינימום של 0.25” משולי הכרטיס) וכאשר מדובר על פנל (ראה כלל מס’ 2) יש למקם את נקודת הייחוס על הכרטיס עצמו ולא על שולי הפנל. יש לשים לב למקם נקודות ייחוס גם בקבצי ה- SolderPaste לטובת שימוש במכונות מריחת בדיל (Printer) אוטומטיות. כמו-כן, כדי שנקודת הייחוס תהיה ברורה וקלה לזיהוי במהלך שימוש במכונת ה-X-RAY, יש לשמור על אזור נקי מהצד השני של הכרטיס עבור נקודות הייחוס כיוון שקרן הרנטגן חודרת לכל עובי הכרטיס.
7. בדיקת מעגל בסיום עריכה באמצעות תוכנה ייעודית
ישנן הנחיות רבות בתכנון מעגל אלקטרוני לייצוריות ובמאמר זה ניסיתי למנות את המרכזיים שבהם. יחד עם זאת, יש לזכור שגם אם נעבוד לפי כל הכללים, אנו עלולים לבצע שגיאות. לכן מומלץ מאוד לבצע בדיקה לקבצי התכנון באמצעות כלים מתאימים. ישנן מספר תוכנות בדיקה טובות בשוק דוגמת GENESIS, VALOR ועוד. תוכנת VALOR באמצעות הכלי החדש שלה PCBFLOW, (איור 3) מאפשרת לבצע בדיקה לקבצי עריכה בהתאם לעשרות אלפי חוקי תכנון בתוך 2 דקות בלבד. תוצאות בדיקת המעגל כוללות מספר פרמטרים מרכזיים דוגמת: קצרים (Shorts), נתקים (Brakes), התקרבות רכיבים (Component Clearnce), קווים לא מחוברים (Dangling), מרחקי מינימום של ציפוי מעגל (SolderMask Bridge), יחס בין קוטר קדח ועובי מעגל (Aspect Ration), סילקים בתור הפד (Silk on Pad) ועוד ועוד…בדיקה מסוג זה, תאתר לנו שגיאות בתכנון בצורה מהירה וידידותית ותמנע תקלות ייצור לא נעימות.
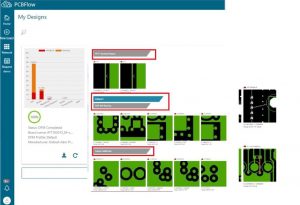
איור 3: הרצת דו”ח בדיקת מעגל ליצוריות (DFM/DFA) בכלי VALOR של חברת SIEMENS מאפשרת לאתר שגיאות בשלב תכנון הכרטיס האלקטרוני. קרדיט: ניסטק דיזיין
לסיכום, בשלב תכנון ועריכת הכרטיס האלקטרוני יש להתחשב בשיקולי ייצור והרכבת המעגל. תכנון נכון ליצוריות מונע שגיאות בתהליך הייצור, מקצר את זמן היציאה לשוק, מוזיל את עלות הייצור ובסופו של יום מניב רווחים טובים יותר לחברה. ביצוע התכנון בהתאם לכללי ייצור נכונים, מסייע להצלחת ייצור והרכבת הכרטיס האלקטרוני. על המהנדסים ועורכי המעגלים המודפסים להיות ערים ולהכיר היטב את הטכנולוגיות השונות ברצפת הייצור ולאור זאת, לתכנן את הכרטיס האלקטרוני. סוד ההצלחה טמון בסינרגיה בין תכנון הכרטיס וייצורו.
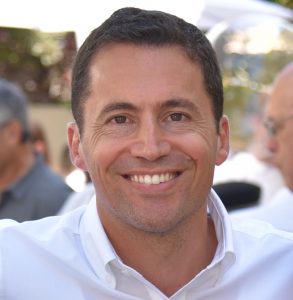
ארבל ניסן, מנכ”ל ניסטק דיזיין קרדיט: ניסטק דיזיין