הירידה בממדי השבבים והעלייה במורכבות שלהם הובילו בשנים האחרונות לעלייה משמעותית בכמות הבדיקות הנדרשות בעת ייצור השבבים, ולמעשה נוצר מצב בו מכונת המדידה צריכה להיות מדויקת יותר ממכונת ייצור השבבים. לעובדה כי השבבים עומדים בסטנדרטים הנדרשים וכי לא נפלו בהם פגמים בתהליך הייצור – יש כמובן חשיבות כלכלית עצומה. בנוסף, יצרני השבבים מפתחים תהליכי ייצור של מבנים ננו-מטריים תלת-ממדיים. הטווחים האפשריים (Tolerance) של מכונות הייצור יורדים. לדוגמא, מיקום שכבה על שכבה קודמת חייב להיות בטווח של ננו-מטרים בודדים. מכונת מדידת מיקום שכבות(Overlay Metrology) מייצרת מידע המאפשר לכייל את מכונות התהליכים: החל מתהליך הליטוגרפיה, ויתר התהליכים הכימיים כמו איכול ונידוף, כדי להגיע למיקום סופי של מאות השכבות הנדרשות בשבב האלקטרוני.
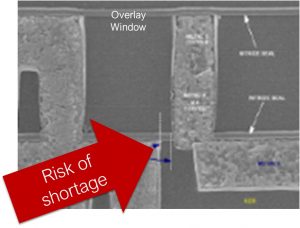
התמונה ממחישה את הצורך במדידות ה- .overlay
קרדיט: צילום יח”צ
האתגרים הכרוכים בביצועי מכונות המדידה, וכיווני פתרון אפשריים:
-
יכולת מדידה מדויקת בעלות סבירה
נדרשות טכנולוגיות שונות למדידת מיקום שכבות. נעשה שימוש במכונות אופטיות באורכי גל מתאימים, מתחומי XRAY לאורכי גל בתחום אינפרא-אדום, וגם במכונות מבוססות הדמיה באלקטרונים. לכל טכנולוגיה ישנם יתרונות ומגבלות. מכשירים אופטיים מהירים יותר, עלותם סבירה, אך ישנה בעיה הולכת וגוברת של דיוק המדידה.
-
שינויים בתהליכי הייצור, זניחים מבחינת יצרן השבב, משנים את תוצאת המדידה
הרכיבים התלת-מימדיים מאד מורכבים ולכן במהלך הייצור, לא פעם, המבנה שלהם משתנה. חלק מן השינויים אמנם לא מזיקים לשבב העתידי אך בהחלט מפריעים למכונות המדידה. כך לדוגמא, אם העובי של השכבה ישתנה – השבב ישאר תקין אך הבדיקה תיפגע.
אתגר זה מחייב פתרונות המתבססים על פיזיקה מורכבת כמו למשל שימוש באורכי גל שונים, או שימוש במיקרוסקופ אלקטרוני וזוויות שונות של הקרנת אלקטרונים. פתרונות המלווים בהרבה אלגוריתמיקה ועיבוד אותות במטרה לסנן רעשים.
-
רעש מובנה במערכת המדידה
מערכות המדידה עצמן כוללות גם רעש מובנה בתוכן הנובע מאלקטרונים של חיישנים או מרעשים מכניים. לדוגמא, יכול להיווצר מצב של רעידות הנוצרות כתוצאה מהשפעות תרמיות. למעשה, מספיק שהטמפרטורה תעלה במעלה אחת – כדי שהסיליקון יתפשט ביחס של 3 למיליון. אם לא נדע למדל את ההתפשטות הזאת ולקחת אותה בחשבון מראש, בשלבי התכנון והכיול של המכונה – אזי המכונה לא תוכל לבצע מדידות מדויקות.
-
שינוע מהיר גורם לרעידות
עוד סיבה להיווצרות רעידות מקורה בצורך לשנע את פרוסת הסיליקון מתחת למיקרוסקופ האופטי בצורה מהירה מאד. שימוש בפתרונות מכניים ואלגוריתמים-פיסיקליים יכולים לסייע להתגבר על האתגר. למשל, צילום במהירות גבוהה מאפשר לצלם גוף בתנועה מבלי שיתבדר, מצד שני חשוב לזכור גם כי כאשר מצלמים מהר מאד אין מספיק אור.
-
רעשים: מכאניים, אלקטרוניים, תרמיים
רעשים אלקטרונים הנובעים מאיכות הגלאים גם מאתגרים את יצרני מכונות המדידה. המינימום האפשרי של להוציא סיגנל תלוי בכמות הפוטונים או האלקטרונים שהמכשיר אוסף, ולכל חיישן יש סף מסוים. הדרך להתגבר על הרעש האלקטרוני היא ע”י ביצוע של בדיקות חוזרות ונשנות ומיצוע של כל הבדיקות. פתרון זה דורש זמן, ומשפיע בסופו של דבר על מחיר המכונה. אם אנחנו צריכים למדוד אלפי נקודות על גבי פרוסת הסיליקון, וכל מדידה אורכת שניה, אז הבדיקה הכוללת של הפרוסה תיקח אלפי שניות – פרק זמן גבוה מדי בעולם שלנו. אם לדוגמא הלקוח מייצר 100 פרוסות לשעה אזי מכונת המדידה לא יכולה להיות החוליה המעכבת בתהליך.
רעשי רעידות פוגעים בדיוקים ומחייבים מערכות בידוד מרעשים חיצוניים או כאלו שנוצרים במכונה. פליטת חום תגרום להתפשטות חלקים במכונה וסטיות במערכות אופטיות – מה שמוביל לשגיאות מדידה.
המענה לאתגר זה טמון במכונות מהירות בעלות מתקבלת, המשלבות מערכות להנעת פרוסת הסיליקון במהירות רבה וקצב הארה, בפוטונים או אלקטרונים, לשם ייצור אות המאפשר מדידה יציבה ומדויקת.
-
ניקיון פסח ומניעת נזקים למוצר הנמדד
אתגר נוסף הוא הניקיון. בשעה שמכונות המדידה שלנו מבקרות את תהליך הייצור של הלקוח הן עלולות במקביל גם לזהם את פרוסת הסיליקון ולעכב את ייצורה. פרוסת הסיליקון עוברת תהליך ייצור נקי מכל רבב, כולל בזמן נידוף של שכבות, איכול והטמעת יונים. מכונות המדידה נדרשות להימנע מלהוסיף זיהומים – חלקיקים ומולקולות העלולים לשנות את איכות השבב.
קרינת מכונות המדידה יכולה לייצר נזק על פני הפרוסה ואף במבנה הפנימי שלה. כך נוצרת מגבלה בשימוש בעוצמת הארה או אנרגיית אלקטרונים כדוגמא.
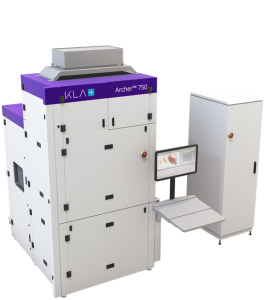
מכונת מדידה Archer 750 ak KLA
-
מניעת הפתעות ונזקים לייצרן ע”י כשל מכונת המדידה
מכונות מורכבות כמו מכונות מדידה מצטיינות באמינות גבוהה מאד על מנת שלא תעצורנה את תהליך הייצור. אולם הלקוחות היום אינם מסתפקים בכך, הם דורשים כי המכונות ינבאו כישלונות עתידיים של עצמן, לפני שהכשל קורה בפועל ומשפיע על תוצאות המדידה.
כך לדוגמא, בזמן שהמכונה נותנת מענה מדויק של בקרת תהליכים, מופיע חיווי המעיד כי יחידת התאורה עומדת לדעוך בקרוב וכי כדאי לתקן אותה כבר עכשיו כדי למנוע תקלות בעתיד. באמצעות בינה מלאכותית המשולבת היום במכונות המטרולוגיה ניתן לחזות מצבים עתידיים אלו, תוך שימוש בחיישנים לאיסוף נתונים שונים לגבי פעילות המכונה.
-
כיול תוך כדי עבודה
המכונה מגיעה לרזולוציה של תת-ננו-מטרים, כיצד מכיילים מכונה כזאת? הכיול של המכונה מחייב שיתוף פעולה בין טכנולוגיות שונות של מדידה, לרבות שיתוף פעולה עם הלקוחות. לכן, הכיול קורה בבדיקות המכונה כבר בתהליך הייצור שלה, ובהמשך על רצפת הייצור הספציפית בהתאמה לדרישות הייצור.
אפשר לומר כי נדרשת היום גישה חדשה לכיול מכונות המדידה. כיול המתחיל בייצור של תת רכיבי המכונה, ואפשרות לאפיין ביצועי תת רכיב בעתיד, כשהוא פועל בתוך המכונה. לדוגמא, מערכת הנעה המדווחת על עלייה בפליטת חום או התגברות חיכוך במיסבי הנעה עקב מחסור בשימון – בעיה קשה מאד בסביבת ואקום.
לסיכום, האתגרים בתחום רבים ומגוונים. חלק מהפתרונות בידינו. צוותים משולבים של מהנדסי אלקטרואופטיקה, חומרים, פיזיקאים ועוד שוקדים יום וליל על פיתוח התחום, זירוז תהליכי הבדיקות והגברת יעילותם ואיכותם. שיתופי פעולה עם מוקדי מידע באקדמיה יכולים לסייע בפיתוח טכנולוגיות מתאימות. גם שיתוף פעולה בין חברות מתחרות יכול לסייע היום להגיע לתהליכי כיול שישפרו את מצבו של היצרן ואף יפתחו שווקים חדשים לכל החברות, כמו למשל, עיבוד מידע ממכונות שונות, בסביבת רצפת הייצור ועוד.
בתמונה: יורם עוזיאל, דירקטור טכנולוגיות ומנהל פיתוח מתקדם בחברת KLA